Benefits of Using CNC Grinding Tools for Unleashing Precision
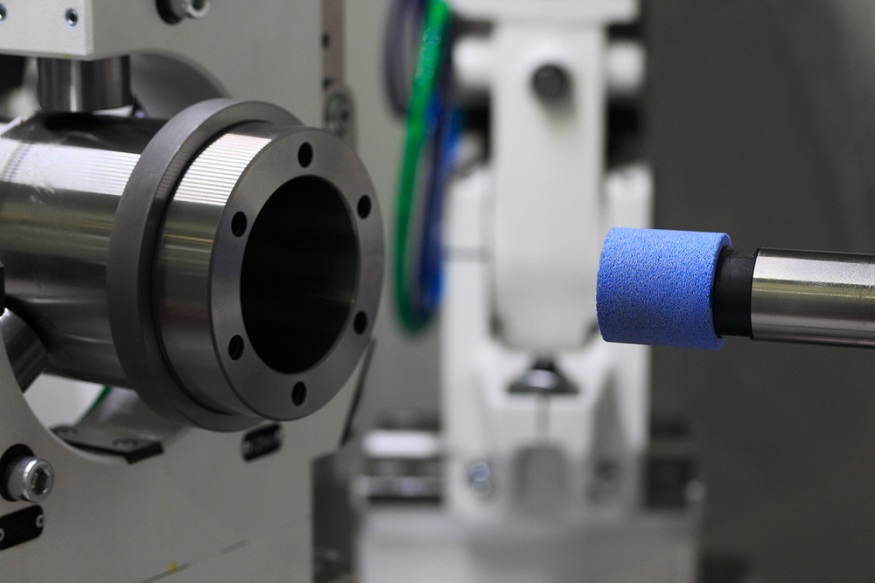
CNC (Computer Numerical Control) grinding tools have transformed the manufacturing landscape by enhancing precision, efficiency, and versatility. These advanced machines automate the grinding process, allowing for the production of intricate components with minimal human intervention. As industries increasingly adopt CNC technology, understanding the benefits of CNC grinding tools becomes essential for manufacturers aiming to improve their operations. In this article, we will explore ten key advantages of using CNC grinding tools, highlighting their impact on quality, productivity, and cost-effectiveness.
1.Exceptional Precision and Accuracy
One of the most significant benefits of CNC grinding tools is their ability to achieve exceptional precision and accuracy. These machines can operate with tolerances as tight as 0.0001 inches, making them ideal for applications that require rigorous specifications. The computer-controlled nature of CNC grinding eliminates human error associated with manual grinding, ensuring that each part produced meets exacting standards. This level of precision is crucial in industries such as aerospace, automotive, and medical device manufacturing, where the slightest deviation can have serious consequences.
2. Consistent Quality
CNC grinding tools are renowned for their ability to deliver consistent quality across all produced parts, a crucial factor in modern manufacturing. Once these machines are programmed with specific parameters, they can replicate the same grinding process repeatedly without any variations in quality. This level of repeatability is particularly essential in mass production environments, where uniformity in parts is critical for ensuring that components fit and function as intended.
By maintaining high standards for every component produced, CNC grinding tools help manufacturers enhance their reputation for quality and reliability. This consistency not only minimizes the risk of defects but also reduces the need for rework or adjustments, leading to increased efficiency in production processes. As a result, manufacturers can meet customer demands more effectively and deliver products that consistently meet or exceed expectations.
Ultimately, the ability to produce uniform parts contributes significantly to customer satisfaction. When clients receive components that adhere to the same high quality every time, they are more likely to trust the manufacturer and establish long-term business relationships. This trust can lead to repeat orders and positive referrals, further solidifying the manufacturer’s position in the competitive market.
3. Increased Efficiency
CNC grinding tools significantly improve operational efficiency. Unlike traditional grinding methods, which require constant supervision and manual intervention, CNC machines can operate autonomously once programmed. This automation allows for continuous production, reducing downtime and increasing output. Additionally, CNC grinding tools can perform multiple operations in a single setup, further streamlining the manufacturing process and saving valuable time.
4. Versatility in Applications
CNC grinding tools are incredibly versatile and can handle a wide range of grinding operations. Whether it’s cylindrical, flat, internal, or precision grinding, these machines can adapt to various applications and materials. This flexibility allows manufacturers to optimize resource utilization and quickly respond to changing production requirements. The ability to switch between different grinding tasks without significant downtime is a significant advantage in today’s fast-paced manufacturing environment. Ultimately, the ability to handle a wide range of grinding operations positions CNC grinding tools as essential assets in modern manufacturing, driving both efficiency and competitiveness.
5. Enhanced Surface Finish
CNC grinding tools are capable of producing superior surface finishes compared to traditional grinding methods. The precision and control offered by CNC technology allow for finer cuts and smoother surfaces, which are essential in applications where surface quality is paramount. This enhanced surface finish not only improves the aesthetic appeal of the parts but also contributes to their functionality, reducing friction and wear in mechanical components.
6. Reduced Waste and Material Utilization
The high precision of CNC grinding tools leads to reduced material waste during the machining process. Because these machines can produce parts with minimal errors, there is less scrap material generated compared to manual grinding. Additionally, the ability to achieve tighter tolerances means that manufacturers can utilize materials more efficiently, ultimately lowering production costs and contributing to sustainability efforts.
7. Safety Features
CNC grinding tools are designed with numerous safety features that enhance the working environment for operators. These machines often include safety guards, emergency stop buttons, and monitoring software to prevent accidents. By minimizing the risk of operator injury and equipment damage, CNC grinding tools create a safer workplace, allowing employees to focus on their tasks without unnecessary concerns about safety.
8. Simplified Training and Operation
Operating CNC grinding tools generally requires less specialized training compared to traditional grinding methods. While operators still need to understand programming and machine setup, the complexity of manual skills is significantly reduced. This simplification makes it easier for manufacturers to train new personnel and allows for a broader range of employees to operate the machinery, ultimately improving workforce flexibility and reducing labor costs.
9. Adaptability to Design Changes
CNC grinding tools can be quickly reprogrammed to accommodate design changes or new part specifications. This adaptability is crucial in industries where production requirements can change rapidly. Instead of investing in new equipment for different parts, manufacturers can leverage their existing CNC grinding tools to meet evolving demands. This capability not only saves time and resources but also enhances a company’s ability to innovate and respond to market trends.
10. Long-Term Cost Savings
While the initial investment in CNC grinding tools may be higher than traditional grinding machines, the long-term benefits often outweigh these costs. Increased efficiency, reduced waste, lower labor costs, and consistent quality contribute to significant savings over time. Additionally, the durability and reliability of CNC machines mean less frequent maintenance and downtime, further enhancing their cost-effectiveness. By investing in CNC grinding technology, manufacturers can position themselves for sustained growth and profitability.
CNC grinding tools like Swiss-type turning machine have revolutionized the manufacturing industry by providing exceptional precision, efficiency, and versatility. From achieving tight tolerances and consistent quality to enhancing safety and reducing waste, the benefits of CNC grinding are numerous and impactful. As industries continue to evolve, embracing CNC technology will be essential for manufacturers looking to maintain a competitive edge. By understanding and leveraging the advantages of CNC grinding tools, businesses can optimize their production processes, improve product quality, and drive long-term success.