Making Milling Machining Safer – Safety and Risks Assessment
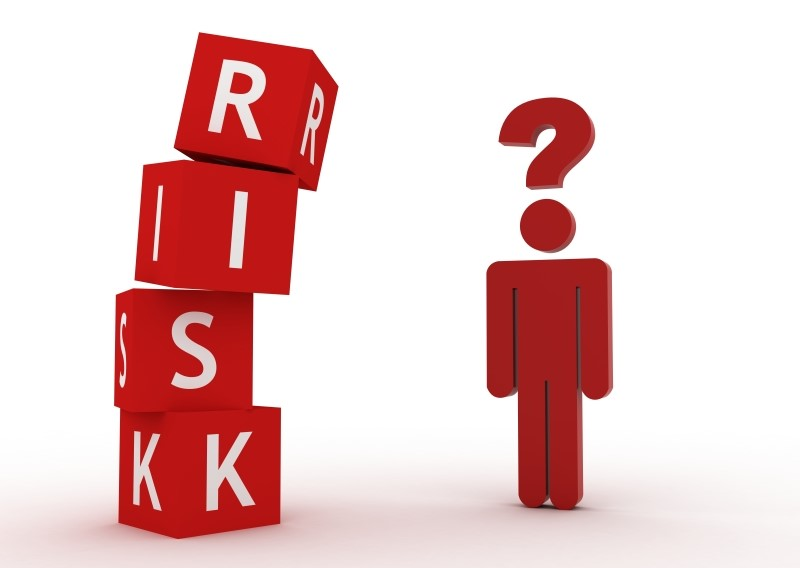
People working at CNC milling services have to undergo a lot of safety measures to avoid any damage in their line of work. Modern technology certainly has made milling tasks safer, but there are risks involved in it that could cause harm to the worker. Most companies following international standards abide by these regulations in their troubleshooting sessions before handling production tasks. The following is a list of potential risks in milling jobs and the solutions for each one of them.
Potential Risk #1
Any operator working while wearing a loose garment or long hair can get caught by the moving parts of the CNC milling machine.
Solution
All operators must wear proper overalls at all times. CNC milling services usually have a standard uniform for their technicians. They also need to wear eye goggles and arrange their hair to cover it with their protective headgear. An operator should never be allowed to wear any form of jewelry when they are handling milling tasks.
Potential Risk #2
The skin of the operator is at risk of getting irritated by industrial fluids such as grease and oils.
Solution
All operators should wear work gloves when they operate a CNC milling machine.
Potential Risk #3
Revolving cutters making contact with any part of your body pose a significant risk for the integrity of the worker.
Solution
All CNC milling machines have an emergency button placed in an easy-to-reach location to make it easy to turn off the device in case of an emergency. This button is also known as “the kill switch,” and it’s mostly used to avoid damaging expensive workpieces. But these safety concerns have made it handy to safe keep the integrity of the workers as well.
Potential Risk #4
Working extra detailed tasks may put at risk the fingers of the operator when he handles the workpiece.
Solution
Operators can avoid direct contact with the machine since the device is equipped with handles, handwheels, and other tools to manipulate the parts being machined without risks.
Potential Risk #5
Operators might experience electrical shocks from the CNC milling machines.
Solution
Established manufacturers isolate their milling machines before adjusting their internal mechanisms. The operators should also wear non-conductive protective gloves while troubleshooting the machine before handling a milling task.
Potential Risk #6
Heavy parts can fall from the work table and cause an injury to the operator or damage the milling machine.
Solution
The milling workshop needs to be thoroughly organized before starting any milling task. Everything should have a place and location, and the working structure should follow a very specific model to avoid this type of mistake. Heavy parts should be handled by more than one operator if it’s needed.
Potential Risk #7
Misplaced items around the CNC milling workshop or slippery floors can cause accidents and pose a risk to the operator.
Solution
The workshop should have a cleanup team with a strict schedule to keep all the working areas clean at all times. Operators should also be instructed to place back their tools in their proper place to avoid littering.
Potential Risk #8
CNC milling machines do not receive periodical maintenance. This can pose a risk to the operator at some point.
Solution
All CNC milling machines have a scheduled checkup after working a certain number of hours. CNC milling workshops need to follow these revisions on time to avoid any issues. Untimely maintenance can be costly in the long run if the workshop has to cover the medical bills of a worker.